How to Select and Train Elite PPF Installers: The Ultimate Guide
5 Steps to Train Top Notch PPF Installers Secrets. yink teaches you all the tricks to build a professional PPF installation team from 0-1, any way you can search all over the net, but just read this one!
When it comes to applying Paint Protection Film (PPF), customers typically encounter two types of service providers: those who cut the film manually and those who use machines. The former demands meticulous skill in the installer, while the latter places more emphasis on the precision of the cutting machine's data. Today, we delve into the world of manual PPF application and explore how to cultivate exceptional installers.
Yink's advice to you is a 1+N recruitment model to quickly develop a paint protection film team that is both professional, efficient, and maximises cost control.
"1+N" strategic recruitment model, i.e. one experienced installer assisting a number of novices, which ensures that the shop maintains a constant flow of fresh blood and avoids losses due to the teacher going out to start his own business
High Wage Recruitment "1"
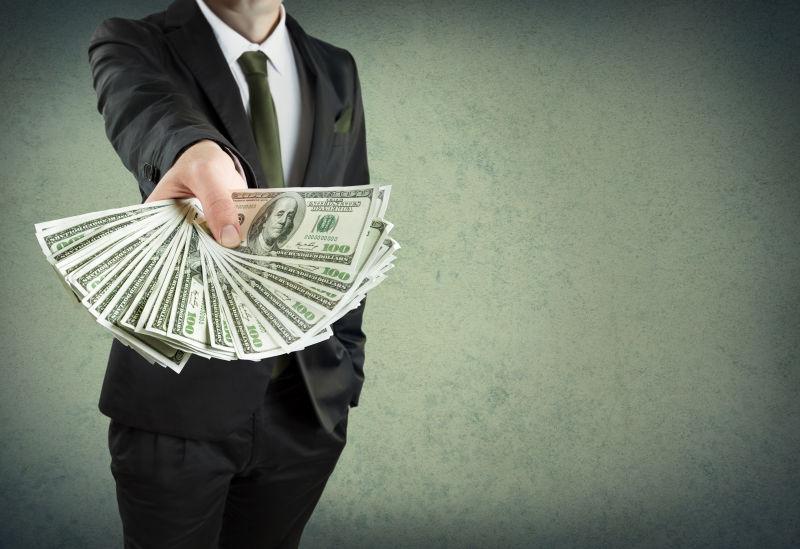
The first step in building a competent team is to hire an experienced professional. Key aspects to consider include:
1. **Installation Experience and Knowledge**: Look for installers with a track record of successful installations across various vehicle brands and models.And they are often able to understand the parts of any hot hatch that are prone to poorly applied paint protection film to focus on avoiding waste, as often the ppf is very expensive, and his high salary is used to save unnecessary waste.
2. **Industry Reputation**: As a long-standing business, the choice of "1" is especially important, and that means you should at least call and ask about their past workplaces, and even visit them to check on the level of customer satisfaction and quality of work they've done before.
3. **Product Knowledge**: Professional PPF installers should also provide detailed information about the products they use. Ask about the brand of membrane they are installing and whether it is a quality product known for its durability and self-healing properties. An experienced installer will be able to explain the different options available based on your budget and specific needs!
4. **Facility Inspection**:The first interview is the perfect time to check out his skills on the job, and it's better to talk than to let him do the work once. It is vital to assess the cleanliness and organisation of their installation. A well-maintained workspace demonstrates professionalism and attention to detail, such as the presence of blisters, drums, etc.
5.**The Importance of Communication Skills**: Knowledge in car paint maintenance and the ability to understand product pain points are also crucial. If, during the process, the PPF installer promotes some cleaning agents or other paint protection products, this can greatly enhance the sales capabilities of your shop. Customers are often more willing to trust the words of a professional PPF installer rather than those of a professional marketer, as it often doesn't carry the same marketing overtone.
6. **Willingness to Share Knowledge**: Some seasoned installers might be hesitant to share their expertise. Offering them a stake in the business could be an incentive.
Recruiting and Training Newcomers, Finding the "N"
Once a seasoned professional is on board, focus on hiring newcomers with these qualities:
1. **Attention to Detail**: Observe their cleanliness and overall demeanor. This trait is crucial for precision work like PPF installation.
2. **Friendly and Communicative**: Ability to interact positively with customers and contribute to sales.
3. **Dexterity and Efficiency**: Look for individuals who are adept and efficient in their tasks.
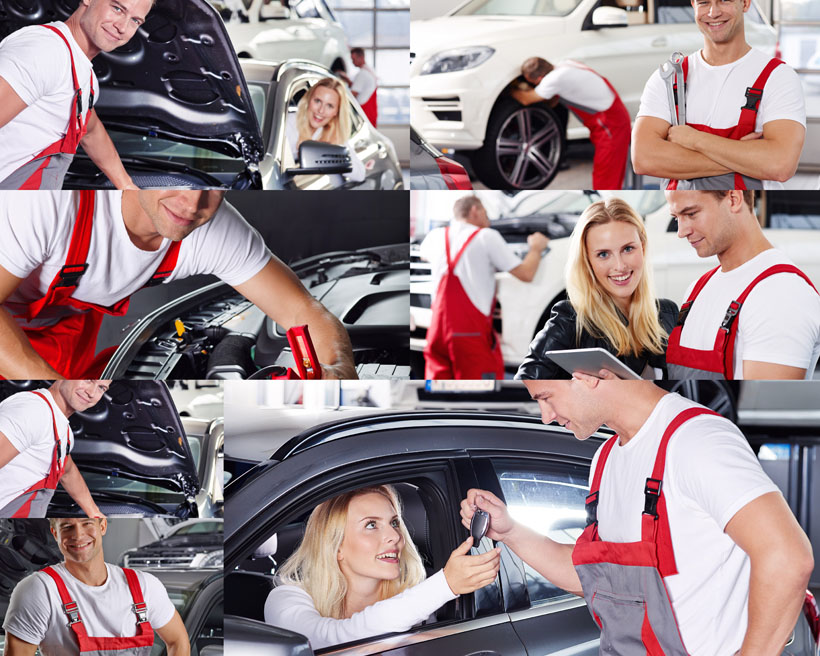
You read that right, it's often as simple as just these 3 priorities in finding N.
Outside of staffing, the workforce needs tools. The tools you need to have on hand are fully catered for in this table below, so remember to bookmark this post before you're ready to set up shop!
**Structured Training Programme**
1 **Initial Training**: Start with a comprehensive training programme covering the technical and customer service aspects of PPF installation. New employees should be familiarised with the different types of PPF, installation techniques and tool usage.
2**Hands-On**: Encourage hands-on practice under the guidance of experienced professionals. Real-life scenarios help hone the skills needed for detailed, precise installations. For example, start with the simple ones first, from the products around you, mobile phone film, interior film, and then progress to full car film, guiding newcomers step by step through the training.
3**Continuous Learning**: The automotive industry is always evolving, so continuous learning is key. Regular training courses should be held to allow the team to understand new PPF materials, tools and technologies, while regularly attending new product launches organised by ppf manufacturers to understand the technical points of posting between each different characteristic of ppf
**Enhanced Quality Control Measures for PPF Installation**
Quality control is not just about setting standards; it's about implementing actionable strategies to ensure these standards are consistently met. Here are specific ways to ensure quality control in PPF installation:
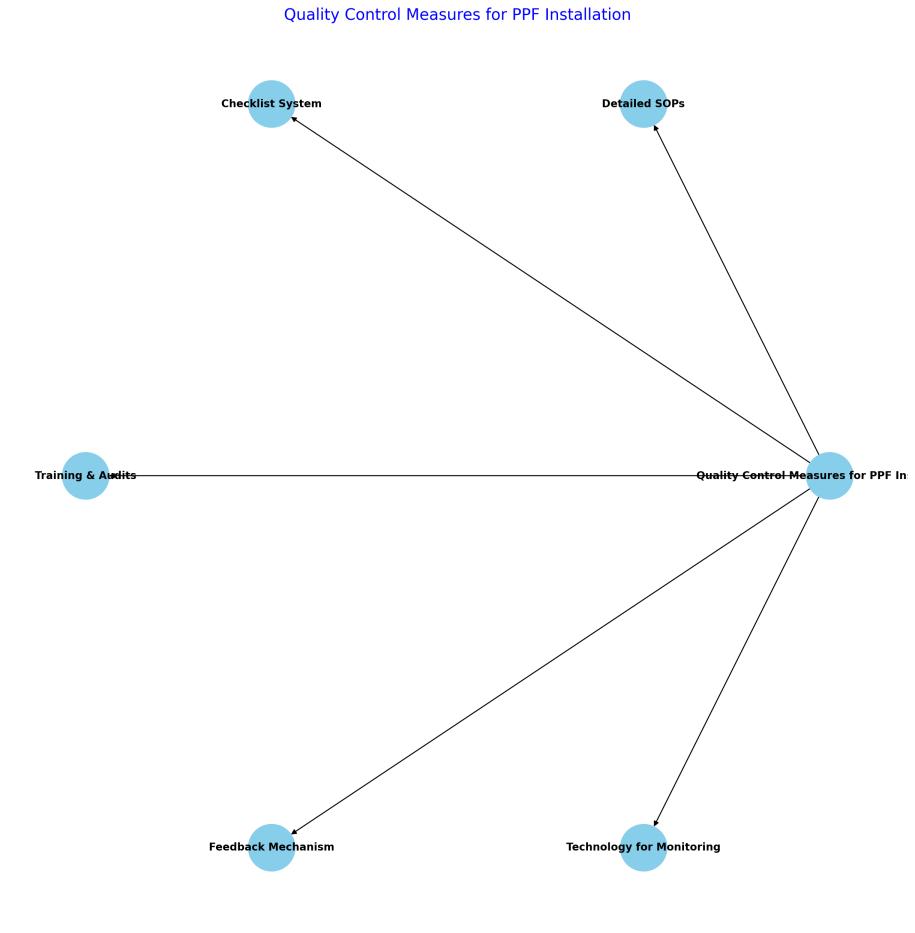
1.Developing Detailed Standard Operating Procedures (SOPs)
- Step-by-Step Guidelines: Create comprehensive SOPs that detail every step of the PPF installation process. This should include surface preparation, film application, finishing touches, and post-installation inspection.
- Visual Aids: Incorporate diagrams, photos, or videos within the SOPs to provide visual references for each step, making it easier for installers to follow and maintain consistency.
2.Implementing a Checklist System
- - **Pre-Installation Check**: Develop a checklist for vehicle inspection before PPF application. This should include checking for existing damage, cleanliness level, and surface irregularities.
- - **Installation Checkpoints**: Create specific checkpoints throughout the installation process where installers must verify that they are adhering to SOPs. For instance, after film alignment, before and after using the heat gun, and final inspection for air bubbles or misalignments.
3.Regular Training and Audits
- - **Training Workshops**: Conduct regular workshops where installers are trained to adhere to the SOPs and are updated on any new techniques or materials.
- - **Quality Audits**: Schedule regular audits where completed installations are inspected by a senior installer or quality control specialist. This helps in identifying areas for improvement and ensuring SOP compliance.
4.Feedback Mechanism
- - **Customer Feedback Forms**: Encourage customers to fill out feedback forms post-installation. This provides direct insights into the customer's perception of the installation quality.
- - **Team Discussions**: Regularly discuss feedback during team meetings, focusing on both positive comments and areas for improvement. Use this as an opportunity for collective learning and refinement of techniques.
5.Utilizing Technology for Quality Monitoring
- - **Digital Reporting Tools**: Use digital tools for installers to record and report each step of their installation process. This can include photos or videos of critical steps uploaded for review.
- - **Performance Analytics**: Implement analytics to track the performance of each installer, identifying patterns in mistakes or areas where additional training might be needed.
6.Customer Education and Engagement
- - **Informative Sessions for Customers**: Train your staff to educate customers about the benefits of PPF, the installation process, and aftercare. Informed customers are more likely to appreciate the value of your service.
- - **Upselling with Expertise**: Encourage your installers to knowledgeably recommend related products or services that could enhance the customer's vehicle protection, such as specific cleaning agents or additional protective coatings.
- **Building Trust**: Genuine, informative interactions build trust. Customers are more likely to return and refer others when they trust the expertise and advice of their PPF installer.
By implementing these detailed training steps, you will have a professional, efficient and money-saving PPF construction team. Great shops are always strikingly similar, and shops that don't do well each have their own problems. We hope today's content has helped you, if you think we've written a good article, please fill out the form below to subscribe to us and we'll give you a 5-day trial of YINK SOFTWARE.
Post time: Dec-21-2023